We can’t believe we are saying this. After fifteen years of printing our own fabric, we have decided to stop. We had to spend some time going over the pros and cons of continuing printing on our own, so we thought we’d share our thinking with you. It was one of those momentous occasions that required a drink. Kris had an orange cosmo and Deb had a mojito. It was happy hour, so we shared an order of gyoza. (By the way, we highly recommend the restaurant for drinks and bites. It’s called Aji in El Dorado Hills, CA.)
Cost of Dyes
Let’s start out with the last reason. We were pretty certain we could get the broken printer to work again (see below for printer woes), but we had run out of the reactive dyes to perform the tests. Our printer requires seven colors. It used to cost a reasonable amount because we could buy the dyes in 250 ml bottles. No more. Because we prefer using the Huntsman Novacron fiber reactive dye (less particulate matter, a phrase we’ll probably never use again), we would now have to buy two-liter bottles. If the idea that we couldn’t use up two liters of dye before it started to degrade wasn’t enough, the idea of coughing up over $2000 for a set of dyes pretty much made our eyes glaze over. This was indeed the final straw. But there really was more to our decision than just dye.
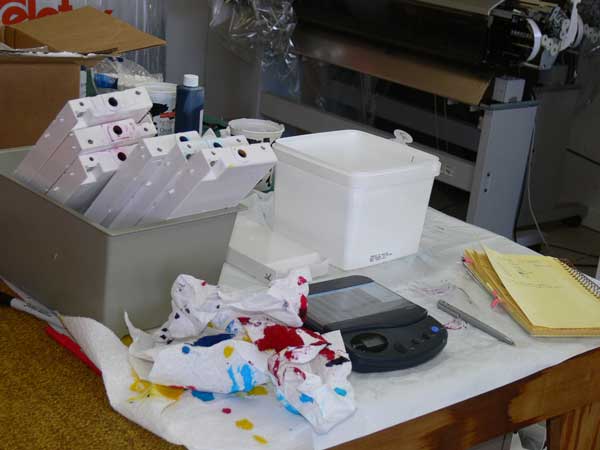
Cost of Repairs
We bought two Epson 9600 wide-format printers over the years. We started using one printer to print and the other to cannibalize for parts. It was a good system that stretched the life out of the #1 printer. Well, we started to really feel the pinch when Epson stopped producing the 9600 print head. We went to China for aftermarket print heads, relying on Dave, our tech guru (and Deb’s husband), to hunt them down. That lasted a few years, but they are now almost impossible to find. Add to that our disaster of trying to upgrade to a newer and less dye-friendly printer and our own forays into printer repair (Deb loves to take things apart, so she got pretty good; Kris was always good at keeping the screws organized), and we knew the end was near. We are going to miss Fadi, our printer repair guy. He made house calls (you have to with printers this large), and we always had a good laugh when he was around. If you live in our area, we recommend him for your printer repair needs (916.334.7875).
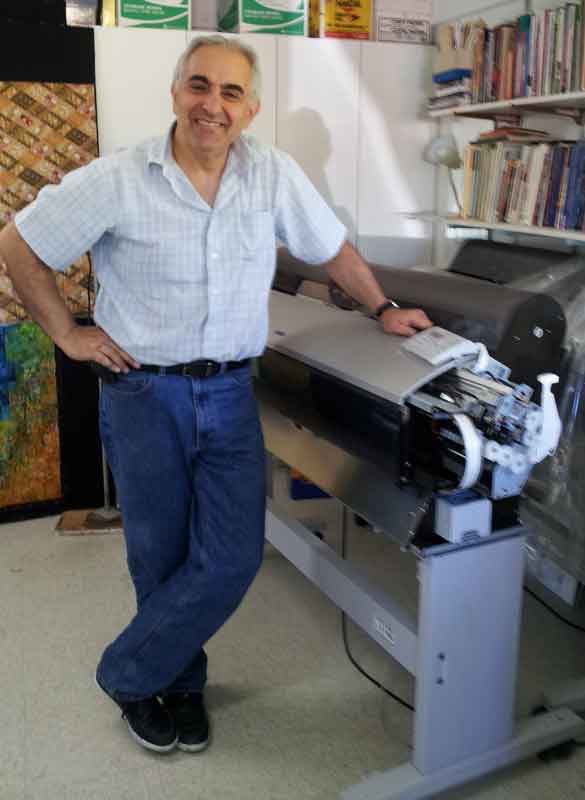
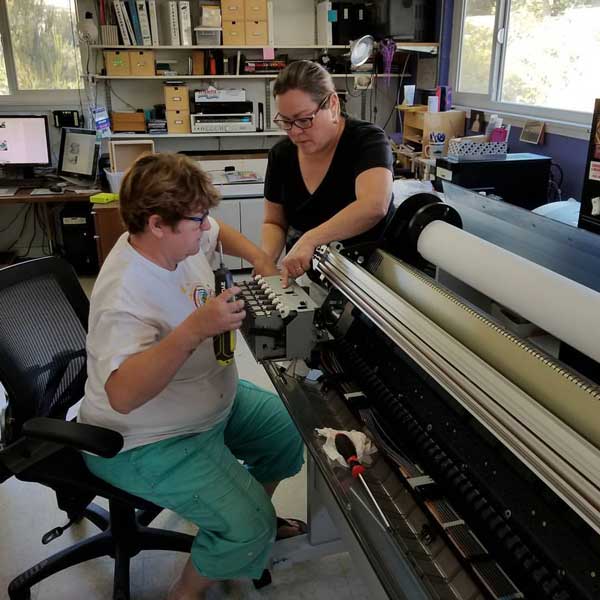
Cost of Fabric
Some of you will realize that most of us fabric people don’t stop to calculate how much we spend on fabric, but when you’re ordering ROLLS of fabric, even the space it takes up starts to make an impression. (More on that in a future blog post.) We have always ordered our fabric from Jacquard Inkjet Fabric Systems, so we are really going to miss Sandy, Jacquard’s office whiz. She always kept such good care of us.
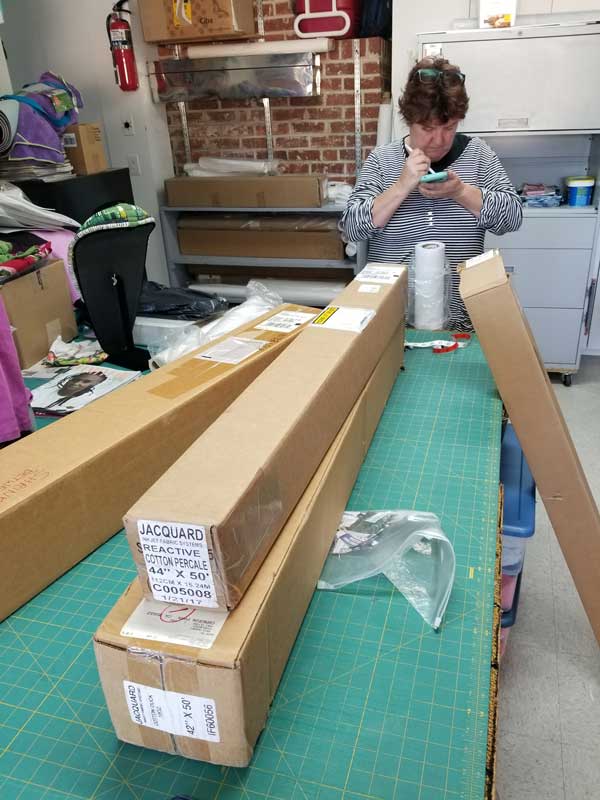
Other People do It Just as Well
We’ve been blogging and publishing on the rise of good — and we mean seriously good — custom fabric printing companies for a while now, so we have decided to take our own advice. We have lots of samples from various companies, so we feel good about going to any number of them to have our own work printed. Click here to read more about fabric printing companies. So why didn’t we do this earlier? For one, sometimes we’d just get in the mood for some fun printing, like the time we made mini bolts of fabric to go in our friend’s doll house sewing room. Yes, our friend’s a San Francisco Giants fan! Kris was so impressed that Deb even remembered to add selvage to the fabric. But read on!
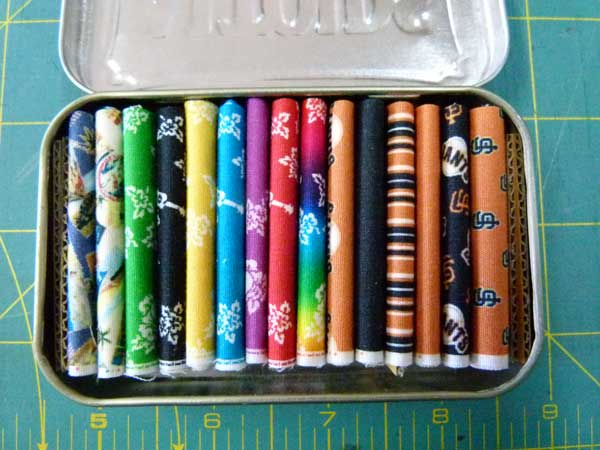
Control, Control, Control
At Pixeladies, we don’t have just one control freak, we’re BOTH control freaks. You can only imagine how satisfying it was to control every aspect of the printing process. We had developed systems to account for the color changes in printing, steaming, rinsing, and washing. We determined when we were going to print. We determined whether the print was satisfactory or not. (And we did sometimes print three or more versions of the same file.) Of course, none of this worked out when the printer was broken, and that was happening with more and more frequency. So what control did we have in the end? And come to think of it, it wasn’t that much fun to have to tweak the file twenty times to get just the right color (because we could). And the steaming, rinsing, and washing was never high on our list of fun things to do. We just might get used to all the time we will save. For now, it’s on to a new way to create fabric!
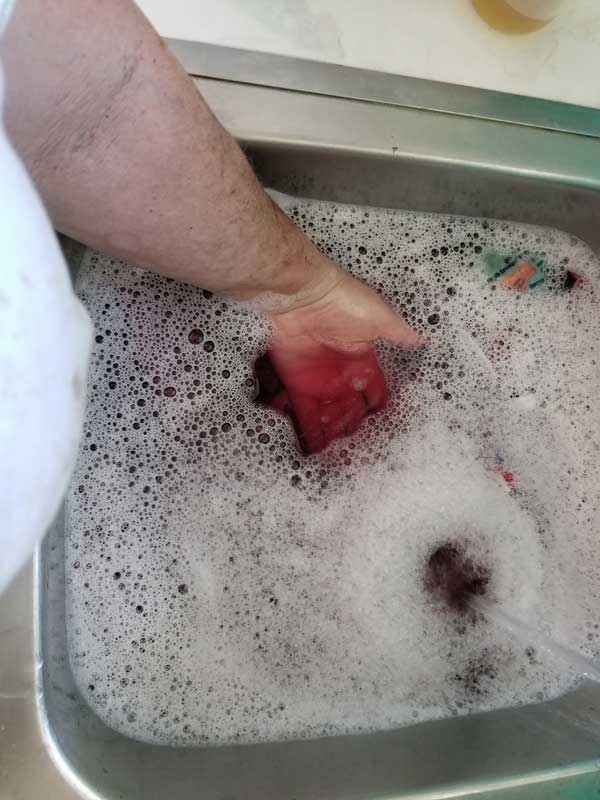
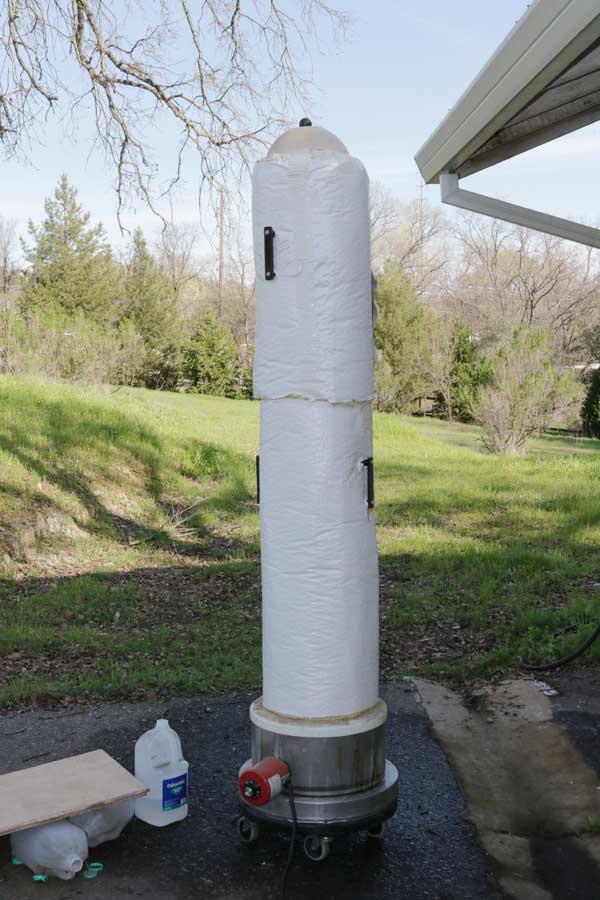
6 responses to “Tech Tuesday: Why We Stopped Printing Our Own Fabric”
Wow! So glad I have some of your pieces from what will now be “the olden days.”
You’re funny, Marcia, but we were actually thinking the same thing, too. It’s just the end of an era and the beginning of a new one!
What great timing, gals! I am just about to lead our local SAQA pod here in Toronto through the steps involved to print with our local company, DesignYourFabric.ca … your article in the SAQA Journal will be a prominent part of our discussion!
Sorry you are having to make these changes to your process but it may lead you down some exciting new paths. 😀
Cheers and happy printing!
Thanks, Mary. We were quite happy with DesignYourFabric.ca, so your group should be quite happy. We have a video on our fabric printing page that takes you through the steps of creating test prints.
[…] you already know, we have decided to stop printing our own fabric. You can read about our reasons here. However, just because we’re not doing it anymore, doesn’t mean you should stop as […]
[…] you already know, we have decided to stop printing our own fabric. You can read about our reasons here. However, just because we’re not doing it anymore, doesn’t mean you should stop as […]